Secteur industriel - Pharmaceutique
INTRODUCTION
Un bioréacteur, appelé également fermenteur, est un système dans lequel on multiplie des micro-organismes (levures, bactéries par exemple) pour effectuer notamment la bioconversion d’éléments.
La plupart des grandes entreprises pharmaceutiques multinationales utilisent des opérations de fabrication biotechnologiques, tels que des produits plasmatiques, des protéines thérapeutiques, des anticorps monoclonaux, des vaccins et d'autres produits de grande valeur. Cette application concerne les sites Biotech où ils produisent du matériel pharmaceutique par fermentation de micro-organismes. Les organismes sont génétiquement modifiés de sorte qu'ils produisent le produit pharmaceutique requis.Les micro-organismes ont besoin d'un flux constant d'air pour permettre de vivre, de se développer et donc de fabriquer des produits. Ceci se fait dans le réacteur au travers du milieu de culture où les micro-organismes se développent. L’air du fermenteur doit être filtré pour être stérile afin d’éviter toute perturbation du milieu.
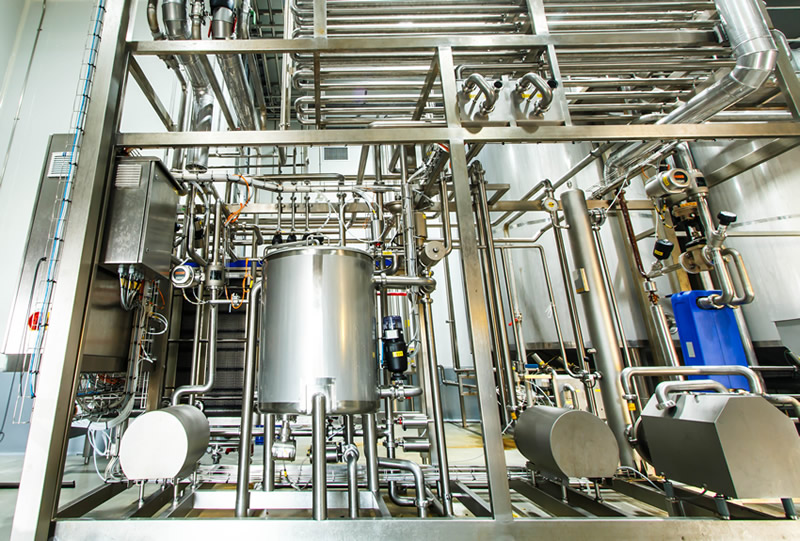
Client : | Multinationale Pharmaceutique |
Localisation : | Allemagne |
RESUME DE L’APPLICATION
Sur ce site de production, de nombreux fermenteurs sont en service. En raison de la nécessité d’avoir des débits d'air très élevés et de très faibles pressions différentielles (pertes de charges), les systèmes d’alimentation d’air (Off-Gas) se composent de grands corps de filtres multicartouches. Suivant la taille de la cuve de fermentation et les débits d’air associés, ces corps de filtres contiennent des cartouches de hauteur 20" ou de hauteur 30".
Au regard notamment du confinement nécessaire (ne pas « casser » la stérilité) de ce process, les filtres doivent durer de nombreux mois.
Pour assurer un fonctionnement économiquement viable et maintenir la stérilité du système, ces filtres sont soumis à de fréquents cycles de stérilisation vapeur in situ.
Par conséquent, les filtres doivent être qualifiés pour démontrer qu'ils sont en mesure de fournir de l'air stérile, qu’ils tiennent plusieurs cycles de stérilisation vapeur et qu’ils génèrent de faibles pressions différentielles.
SOLUTION MISE EN ŒUVRE
Le client utilisait des filtres 0.2µm à membrane PTFE d’un autre fabricant international, dont les spécifications équivalentes chez notre partenaire Amazon Filters sont données par la gamme Supapore TPB.
Nous avons fourni ces cartouches filtrantes de même longueur et de mêmes embouts de raccordement que celles précédemment en place. Cela permettant pour l’utilisateur un remplacement aisé sans aucune modification des installations.
Les filtres, puisque de même efficacité suivant les mêmes normes, ont pleinement respecté le niveau de qualité d’air requis, ont conservé leur performance tout au long des cycles de stérilisation vapeur et remplacent maintenant le produit précédent.
Les avantages pour le client sont un filtre économiquement compétitif et des pressions différentielles inférieures de 30%. Une pression différentielle (perte de charges) inférieure est un avantage important car elle réduit les coûts d'énergie associés à la compression et contrôle de la température de grands volumes d'air.
En raison du nombre élevé de filtres utilisés chaque année, le client avait des exigences d'emballage très spécifiques pour permettre une gestion plus simple par les opérateurs. Nous avons été en mesure d'offrir ces emballages, reprenant le code article du client et les références des réacteurs concernés. Un autre avantage important pour le client est que, en utilisant la proximité de notre logistique, nous sommes en mesure d'offrir des délais plus courts et une plus grande flexibilité dans la gestion des commandes et des livraisons.