Secteur industriel - Sidérurgie
INTRODUCTION
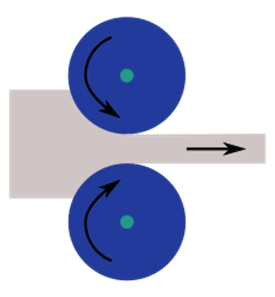
Principe du laminage : le métal subit une réduction d'épaisseur par écrasement entre deux cylindres
Le laminage est un procédé de fabrication par déformation plastique forte et continue.
Il concerne différents matériaux, et notamment certains métaux. Cette déformation est obtenue par compression continue au passage entre deux cylindres contrarotatifs appelés laminoirs. Un laminoir est donc une installation industrielle ayant pour but la réduction d'épaisseur d'un matériau (généralement métallique).
Le site concerné est équipé pour traiter des produits plats en acier inoxydable ferritiques (60 à 70%) et austénitiques (30 à 40%). Ses principales productions se concentrent sur les bobines d'acier, représentant près de 80 % de la production, dont la capacité peut atteindre plus de 300 000 tonnes d'acier par an.
Schématiquement, la « ligne » de production se compose de trains de laminoirs. Ils se composent en général d'un premier ensemble appelé dégrossisseur, puis un train intermédiaire et enfin un train finisseur. Cette « chaîne » permet de passer de barres de grosses sections (billettes) à des fils plus ou moins fins mis en bobines.
RESUME DE L’APPLICATION
Suivant les trains, les vitesses de laminage, les températures, les niveaux de finition sont différents. Par contre, le problème de l'usure des cylindres se pose à tout moment de la production d'un laminoir.
L'usure, en effet, conditionne les changements de cylindres et a donc une influence directe sur la productivité et les frais de fonctionnement. D'autre part, elle peut altérer la qualité du produit laminé en détériorant l'état de surface et la forme du profil en travers.
Depuis de nombreuses années, et afin de réduire les phénomènes d'usure, beaucoup de choses sont axées sur l'amélioration de la qualité des cylindres, sur l’optimisation d'utilisation de l'outil de production et sur la lubrification.
Les exigences de qualité, notamment sur les états de surface, ont nécessité des lubrifiants toujours plus performants et donc toujours plus coûteux. Ainsi, ces huiles fonctionnement en circuit quasi-fermé et doivent donc être filtrées en permanence pour conserver (voire améliorer) sa classe de propreté d’origine (huiles neuves).
Il a donc été développé des systèmes spécifiques avec des éléments filtrants sur-mesure (tant dans l’aspect dimensionnel que dans les embouts de montage) pour pouvoir avoir une durée de vie suffisante entre deux maintenances de chaque train.
Par conséquent, il faut pouvoir fabriquer des éléments sur-mesure ayant exactement les mêmes spécifications que ceux précédemment utilisés et envisager un développement pour des filtres ayant des seuils de filtration plus bas (pour faire face aux nouvelles et futures exigences qualité).
Client : | Groupe sidérurgique mondial |
Localisation : | France |
SOLUTION MISE EN ŒUVRE
En collaboration avec un de nos partenaires, nous avons étudié ces éléments filtrants. Evidemment les aspects dimensionnels, mais surtout la structure, le gradient de porosité,etc… du média filtrant pour être certain que nous pourrions obtenir a minima la même durée de vie.
Nous avons adapté l’outil de production et avons réalisé un moule spécifique pour les embouts. Nous avons ainsi fabriqué ces éléments et avons validé in situ sur les différents trains du laminoir.
En utilisant les connaissances de notre partenaire sur la fabrication des éléments filtrants par technique « meltblown » (extrusion-soufflage), nous avons également pu abaisser les seuils de filtration, sans conséquence rédhibitoire sur la productivité et les coûts de production.